2月15日,2025年中國全固態電池產學研協同創新平臺年會暨第二屆中國全固態電池創新發展高峰論壇在北京舉辦。作為全球領先的新能源智能制造解決方案服務商,先導智能受邀出席,與學界泰斗、產業巨頭共同破解全固態電池產業化密碼。先導智能在論壇發言中指出,全固態電池的產業化是一場發生在設備車間的產業革命,設備生態是決定產業化進程的核心要素。
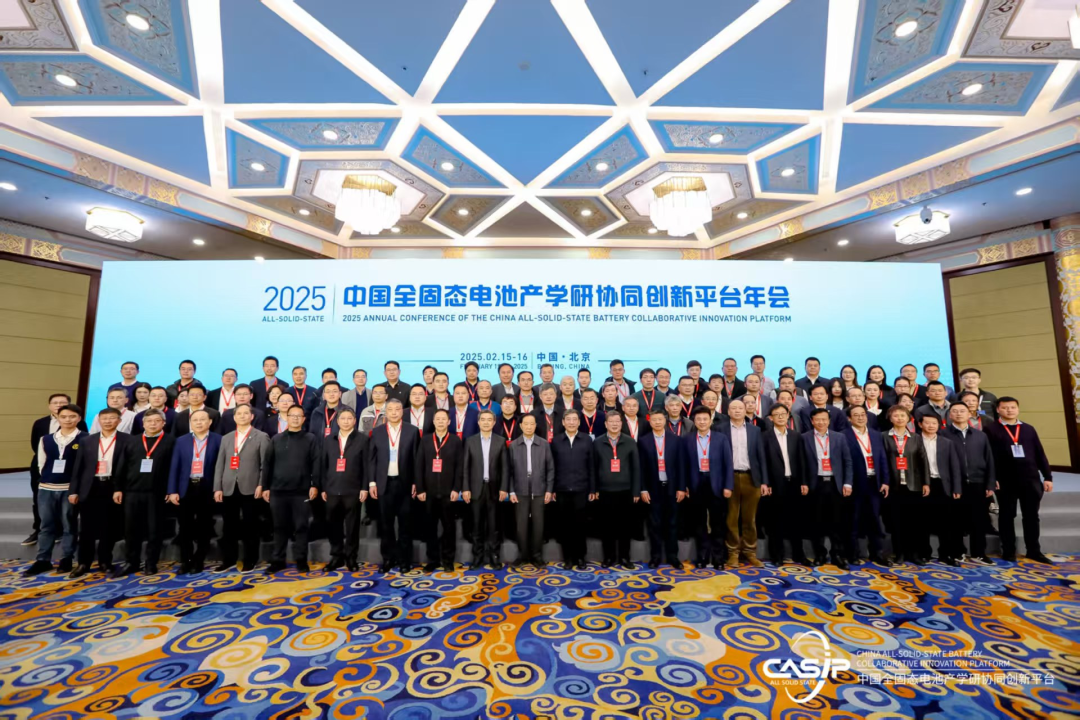
從"搭積木"到"分子料理"
全固態電池制造工藝顛覆升級
論壇上,先導智能表示:全固態電池在制造工藝上與液態鋰離子電池存在根本性差異,看似都是分層結構,但每一層的粘合邏輯和材料兼容性都是完全顛覆的。其技術革新涉及電解質革命、界面工程和環境控制三大核心領域,傳統液態電池產線無法直接升級,需從設備到工藝全面重構。
全固態電池需用固態電解質膜(硫化物/氧化物/聚合物)完全取代液態電解液和隔膜,傳統涂布、壓合設備需徹底改造,如先導智能的干法電極技術和電解質轉印工藝,可實現固態電解質膜的高效制備與均勻貼合,而傳統涂布機就得回爐重造。
液態電池的液態電解質與電極自然浸潤,無需復雜界面處理。固態電池的固-固界面需精密處理以解決“干面包硬拼”的縫隙和阻抗問題,依賴復合粘結劑、相變自填充材料等創新技術,對疊片、等靜壓設備提出“變態級”要求。
很多固態電池的技術路線對生產環境要求極高,如硫化物路線對濕度、氧氣極度敏感,遇濕即釋放毒氣,且易爆炸,對人員安全提出了更高的要求。這要求生產線像半導體車間一樣完全封閉干燥。液態電池的注液車間完全無法達到硫化物路線嚴苛環境的生產標準。
量產不是"單選題"
設備廠商決定全固態電池量產“最后一公里”
關于全固態電池的量產工藝路線,目前業內尚未形成統一的定論,不同的企業和研究機構,可能會根據自身的技術積累和戰略定位,選擇不同的工藝路線。但量產不是“單選題”,而是“多選題”,從長遠來看,技術工藝上仍需百花齊放。
對于全固態電池生產而言,設備廠商決定全固態電池的產業化量產“最后一公里”。
全固態電池的量產,離不開高性能、高可靠性的生產設備。設備廠商只有提供滿足量產需求的高可靠設備,才能保證全固態電池產業化進程不受到影響。
先導智能的全固態電池解決方案之所以領先,是先導和全球頭部電池廠商一起深度共創的結果。通過聯合研發干法電極技術、超薄電解質膜制備等核心工藝,先導實現了全固態電池從電極制備到電池組裝的整線設備全覆蓋,并已獲得很多海內外知名企業的訂單。
在固態電池產業化窗口期加速逼近的背景下,設備廠商需與客戶需構建"技術-工藝-設備"三位一體的聯合開發體系,針對氧化物/硫化物/聚合物不同技術路線,通過實驗室階段定制化驗證(如高精度涂布、真空封裝等工藝適配),快速迭代出兼容多體系、支持高速量產的標準化產線方案。
依托其在鋰電產業深厚的技術積淀與創新能力,先導智能打通全固態電池制造工藝環節,形成了覆蓋全固態電極制備、全固態電解質膜制備及復合設備、裸電芯組裝到致密化設備、高壓化成分容等全固態電池制造關鍵設備的整線解決方案。方案采用了干法電極等先進工藝與高度集成化設計,設備制成工序相對傳統工序大幅減少,并保障多環節嚴格環境管控、產品安全生產。
在固態電池極片及固態電解質膜的制備方面,方案已經達成無需使用溶劑即可實現材料的高效混合與分散混料。其干法成膜復合一體設備可實現連續成膜,在工作狀態時輥跳動穩定在2μm以內,溫度均勻性≤±0.5℃,確保成膜的高度一致性與高效生產。其超薄電解質膜制備設備,具有高生產效率、高生產質量、高自動化等顯著優勢,可實現20μm以下的薄膜涂布。
憑借過硬的產品實力以及高質量的客戶服務能力,先導智能已經與2024年陸續向歐、美、日、韓等國家和地區的頭部電池客戶、知名車企和新興電池客戶交付了各工段的固態電池生產設備。相關產品贏得了客戶的高度贊譽,并陸續獲得重復訂單,成就全球客戶信賴之選。